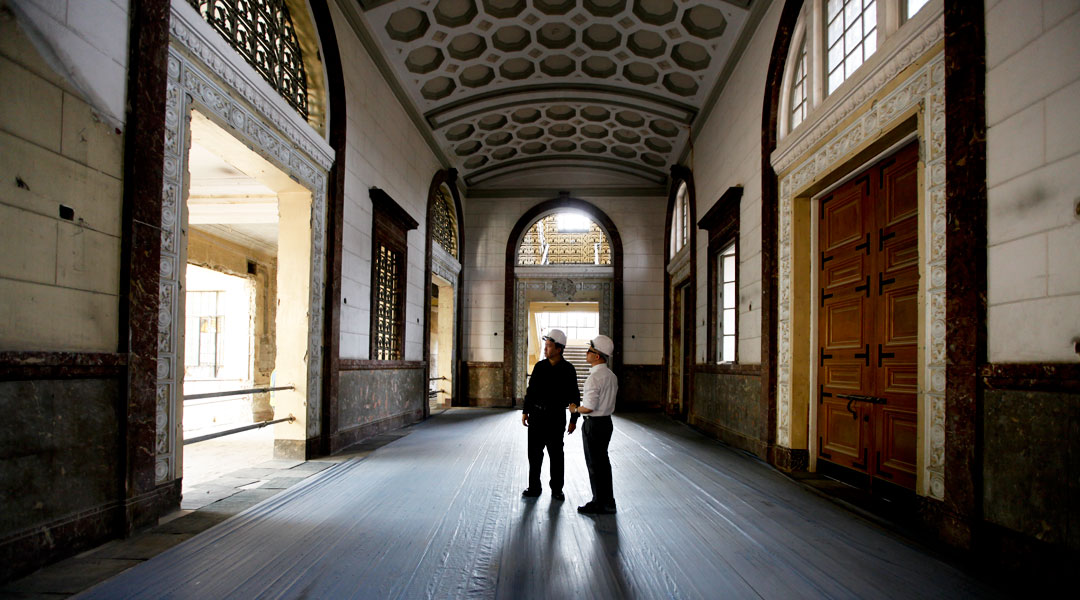
Building the National Museum of Natural History’s Tree of Life
There is a satisfying sense of organic completion in Dominic Galicia and Tina Periquet’s scheme to turn the old Department of Tourism (formerly, Agriculture) building into the nation’s first museum devoted to her diverse flora and fauna. At the heart of the design is a proposal for the transformation of the courtyard into a bright and airy urban space that shall be the hub of the building’s new public realm. A glazed canopy lifted by a steel supporting structure above the courtyard and existing edifice crystallizes this idea, creating both a semi-indoor space and a thematic focal point for the new construction. Dubbed the DNA Tree of Life – this central element is a veritable mission statement for the project. It was born out of, according to Galicia, “the initial sense of the tree as a simple form, something to cover the courtyard. Intuitively we knew that this could work, but we had to find out how.”
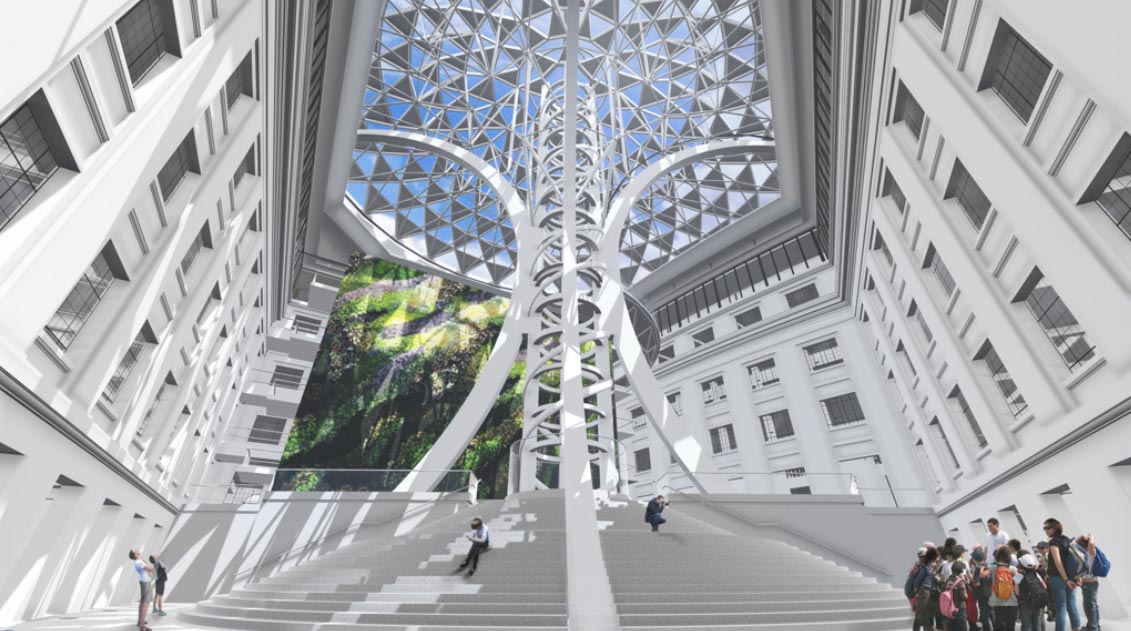
To this end, the aid of world-renowned engineering firm Arup was drafted early during the competition phase. Arup immediately recognized the viability of the DNA Tree of Life, and had since been involved in all surveying, research and engineering aspects of the project.
[one_third padding=”0 20px 20px 0″]
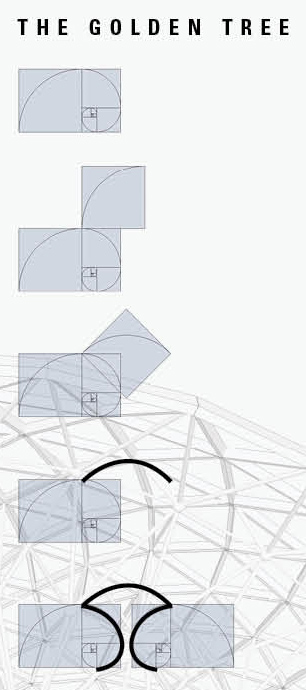
DNA Tree of Life
After the commission for the museum was secured, the design of the Tree went through numerous iterations as a result of the collaboration with Arup. The original concept of the tree profile was generated from the golden section. Each half of this profile can be likened to a letter ‘K’ where the vertical stem delineates a corner of the central elevator shaft, while the diagonal arm and leg morph into one sweeping curve, each envisioned to provide structural support. It was initially conceived that three of these ‘K’s would form the tree. The DNA double helix was then introduced to the composition and represents the commonality among all living things.
READ MORE: A first look at the completed National Museum of Natural History
Diagrid
Arup felt that as it was, the tree configuration was structurally untenable and would prove too expensive. Having extensive experience and great success with diagrid technology (a technique for constructing large buildings with steel that creates triangular structures with diagonal support beams), the structural engineers determined that this was the most viable option to realize the tree. Once this method was accepted, numerous iterations of the tree arose from Arup’s explorations in response to an exhaustive range of considerations ranging from budget to tonnage and everything in between.
Galicia is emphatic about the vital role that Arup plays in the project. “A great deal of thought, effort, and time was expended by Arup into diagrid development and design. We were fully confident that each step we took was valid, always building on what we knew at the time. We got to where we are now only because everything was painstakingly studied and all possibilities were exhausted. Working with Arup allowed us to be fully thorough and fiduciarily responsible.” Eventually, all the possibilities outlined by Arup were presented and the choice was made from these options. This choice was then subjected to bids from various contractors.
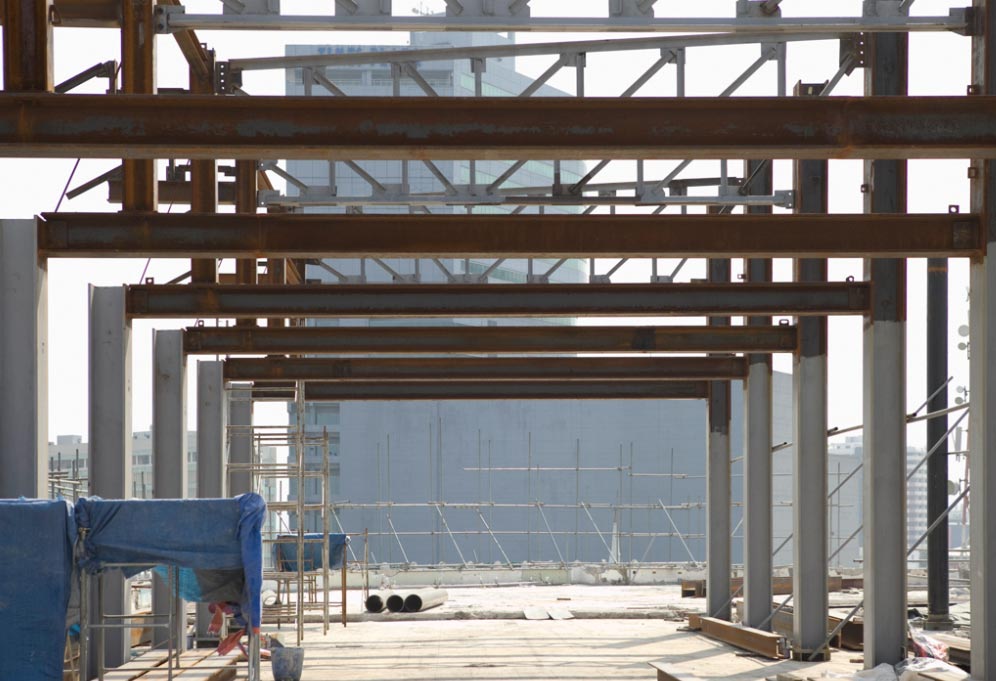
The cost of building any of the diagrid designs still proved too high in the end. One of the bidders though, the partnership of Trans Asia Construction Development Corp. (Philippines) and Nippon Steel & Sumikin Engineering Co., Ltd. (Japan), was confident that it could build the original tree design using the latter’s proprietary technology. This sidestepped the idea of the diagrid altogether, thus allowing the construction to be realized both within budget and time-frame. TransAsia and Nippon Steel were then taken on in a design-build role to deliver the DNA Tree of Life.
NS Truss
In the case of the diagrid, loads can be transmitted along the surfaces of the form to the supporting foundations below. It is an ideal structural system for creating free-flowing, anti-gravitational architectural forms unencumbered by obvious means of support. For the Tree of Life diagrid design, the dome is supported only by a perimeter beam at its base.
The NS Truss by Nippon Steel will now support the canopy directly from underneath. Structural pipes will connect with the saucer’s lattice intersections. These pipes then bolt onto spherical connection nodes which in turn connect with similar configurations to create the structural framing. This system will minimize construction cost and duration, as well as allow for a supporting structure with great flexibility. It’s a serendipitous moment when the technology allows a project to be even more consistent to the original idea, in this case, the presence of a sense of branches and twigs upholding the canopy furthered the idea of a tree, thus allowing the architect to push back towards the initial concept.
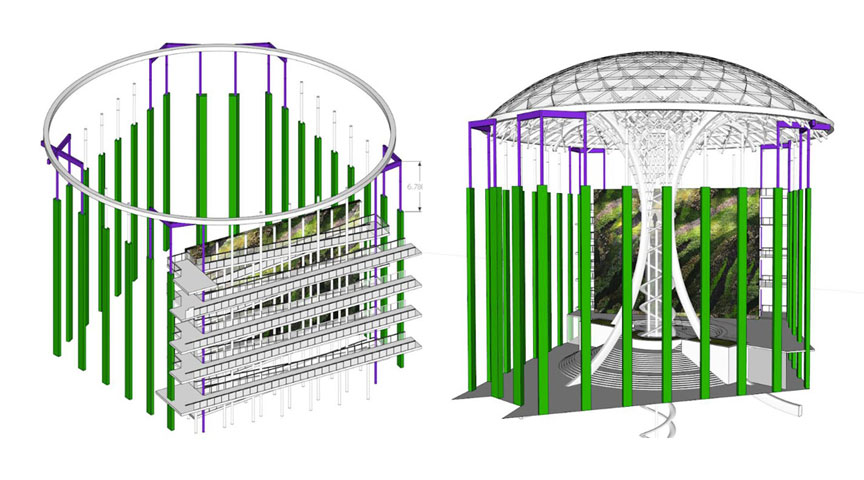
Dome
Early budgetary constraints necessitated a reduction in the diameter of the saucer dome from the original 50-meter span down to 40 meters. As with the general tree design, the dome went through many changes based on Arup’s engineering research resulting in different geometries and grid patterns. Studies of different schemes for the dome lattice ranged from the simple to the complex. One line of inquiry went as far as having concentric fin-like brise soleil to explore possible ways of shading from harsh sunlight. Another lengthy investigation focused on the possible use of ETFE (Ethylene tetrafluoroethylene). This high-performance plastic, outstanding for its light weight, durability and excellent light transmission quality, was considered but was ultimately rejected in favor of glass panels after further studies by ARUP determined that the project would actually benefit from a heavier dome because of greater stability against wind uplift forces.
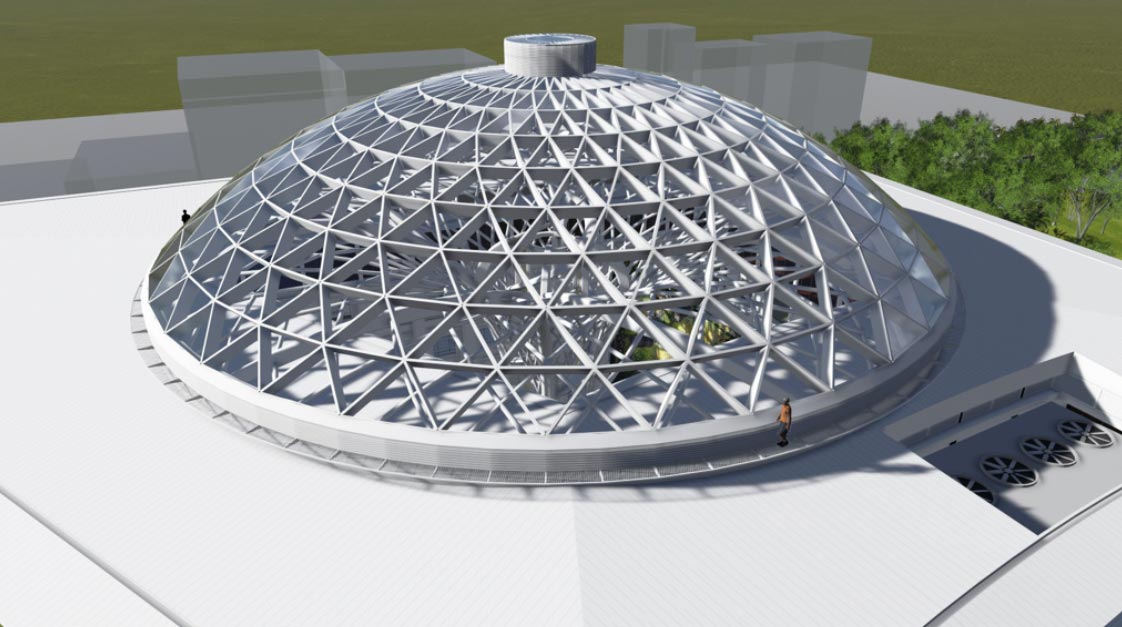
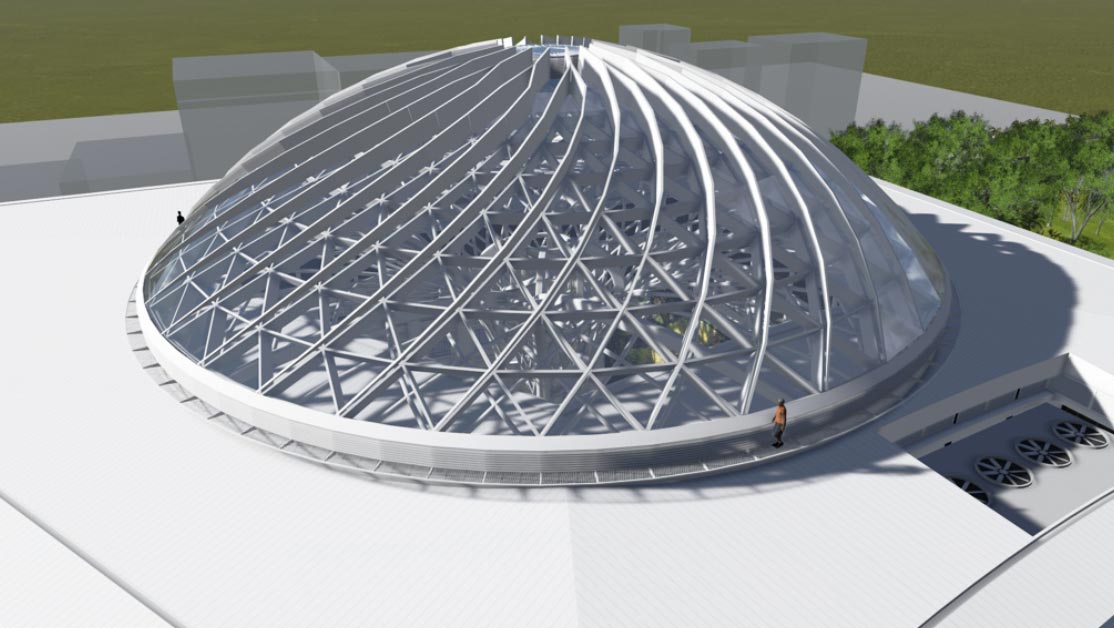
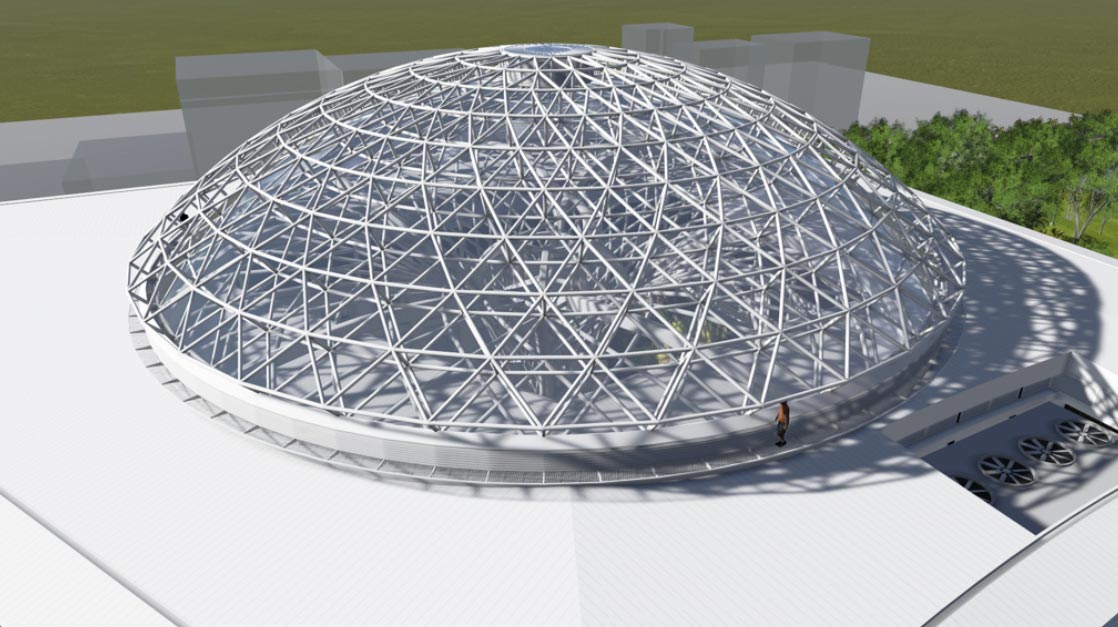
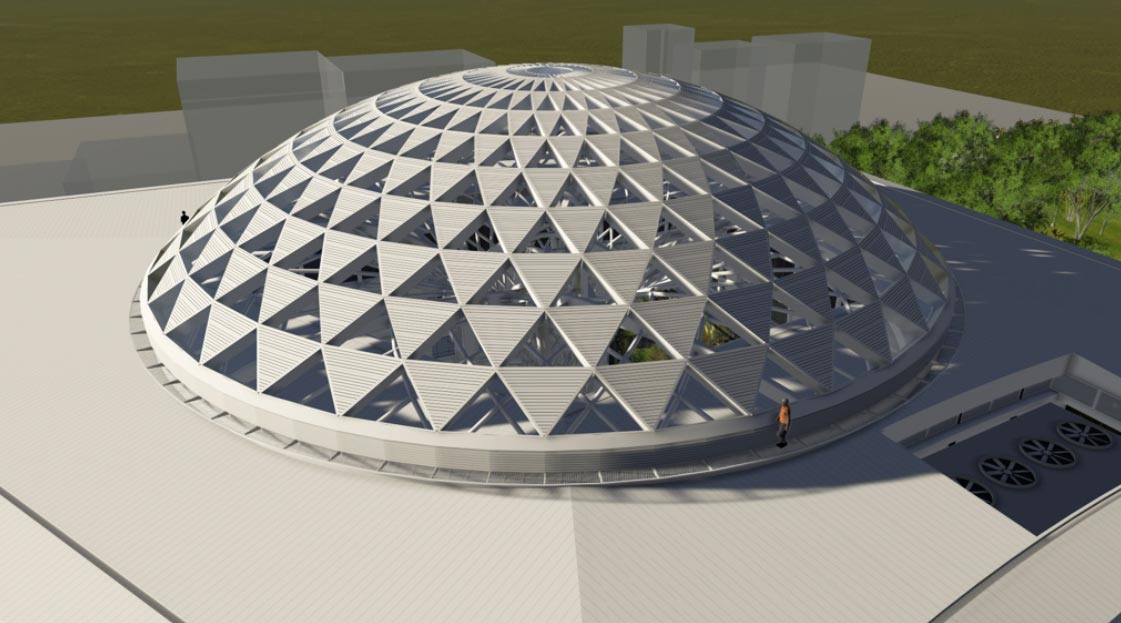
Arup’s explorations generated numerous iterations of the dome based on a wide range of considerations. Scheme A considers the oculus assembly as an exterior element mounted atop the summit. Scheme B explores the possibilities of incorporating radiating fin-like baffles as shading against the harsh tropical sun. Scheme C studies a possibility for optimizing the use of structural steel. Note that the oculus stack now recedes into the dome. A fusion of the two domes in the scheme yielded the final form of the saucer canopy.
This episode led to the exploration of the possibilities for the use of two domes: a glass-paneled inner dome and a fragmented outer dome of triangular fretwork and metal panels. The designers were taken by the look and opportunities this presented, and soon realized that the features of the inner and out domes could be combined in one saucer. The resultant tree canopy will suffuse the interior with an appropriately evocative leafy dappled light.
Oculus
Arup’s Computational Fluid Dynamics and daylighting studies provide vital guides in ensuring that the courtyard remains a comfortable place. The CFD revealed the presence of dominant heat zones directly beneath the dome. Although the means for addressing heat gain was already suggested in the design by the continuous vents sandwiched between the double roofs of the new 6th floor, it was determined that any further features to help vent the dome at its summit would greatly benefit the space. It was at this point that the oculus, initially a purely visual presence, was enlisted to provide the solution to the problem of venting the rising hot air and to minimize the risk of overheating in the courtyard, especially in the upper regions of the space.
Trunk
With the technology made available to the architects by Nippon Steel, a return to the original scheme became fully possible. The legs of the tree, which disappeared completely by the end of the diagrid exploration, were determined absolutely necessary by Nippon for stabilizing the tree under seismic conditions. The three legs of the original scheme became four for maximum stability. This also allowed for the cardinality in the tree’s orientation—a plus in the designer’s eyes as these further this central element’s potential to make connections with the world outside.
The vertical columns at the center of the configuration were initially meant to outline the shaft along which the glass capsule of the elevator would travel. NS technology will now use these as the main support for the entire tree structure. It is important for the tree and the heritage building to be independent of each other and they do not touch at all. The building and the tree will move independently of each other during earthquakes.

Double Helix
The double helix represents our shared DNA and is the central concept of the scheme. It was initially intended for the double helix to be structurally integrated to the tree. Investigations by Arup showed though that this would be problematic as the tree form would have been subjected to unwanted torque forces. Though no longer structural in the final scheme, the spirals provide a dynamic sense of connection between the tree canopy and its roots, the central space and the galleries surrounding it, the courtyard floor and the skies above.
Elevator
The dynamic aspect of the tree, one that affords and completes its experience, is the elevator. It is custom fabricated by the company MP (MacPuarsa) Lifts S.A. (Spain) and, with the exception of the floor and a discreet control panel pillar, is made completely out of glass. This glass capsule only makes two stops and should provide an exhilarating experience along the museum’s processional route.
New Foundations
Providing new foundations upon which to build the DNA Tree of Life presented a unique challenge due to the fact that the new structure is meant to occupy space surrounded by an existing heritage building. Regular pile foundations are hammered into the ground and create strong vibrations. Since this could prove damaging to the older surrounding edifice, utilizing the standard method was out of the question. But once again, Nippon Steel provides the answer. Their Eco-Pile system differs from the traditional as these are screwed into ground. This minimizes any disturbance to the immediate surroundings, as there is no impact or vibration generated. Furthermore, this piling method requires no cement, doesn’t displace soil, and requires far fewer machinery and vehicles than are used in other piling methods, thus reducing cost, work hours and labor. A total of 132 piles were installed in support of the tree alone, providing very strong roots indeed.
The piling machinery used for this technique is small and compact, thus eliminating the need to enlarge the openings on the landmark edifice. Galicia muses, “It’s not just about building technology but also the enabling of something to be done, where there exists a technology necessary to make the technology happen.”
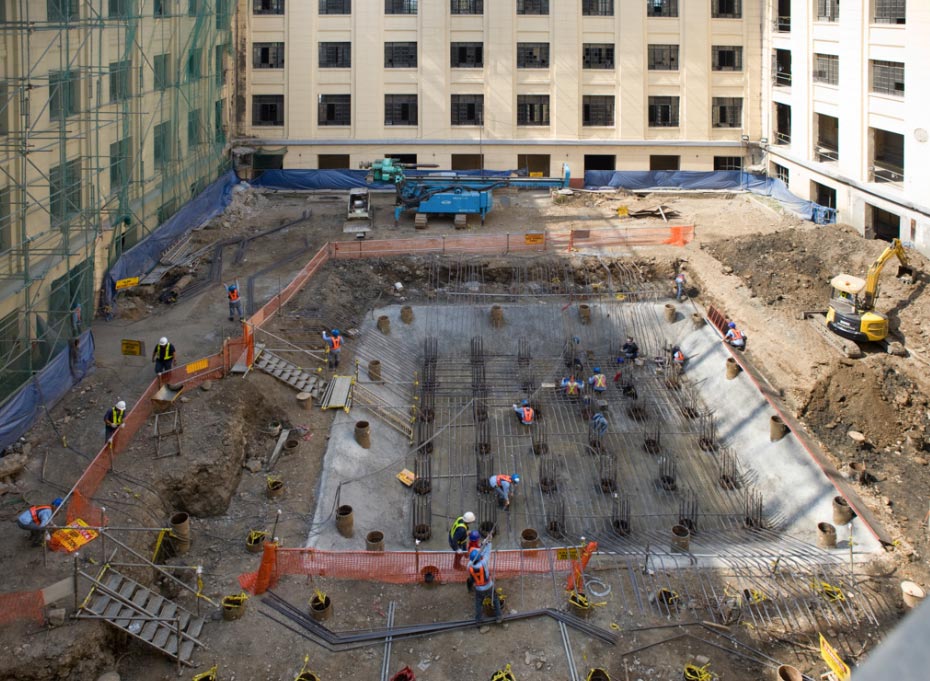
Coming Full Circle
Tina Periquet is just as happy to get back to the original scheme after all the different explorations. It is, after all, what sold the entire concept. And there is the satisfaction in knowing that they have gone through the process of exhausting every possibility, supported by solid science. Due to the scope of the project, it is important to have that science to back up each and every decision.
Retrofit
Arup conducted extensive studies of the old structure and concluded that it is robust in terms of gravity and can withstand the new loading conditions. It was found to be rather weak, though, when it came to seismic considerations. Arup’s seismic retrofit comes in to address the issue. All beams and slabs were stabilized with carbon fiber reinforcement. Walls and columns were concrete jacketed with thin sheer walls from the foundations all the way up to where they prove to be useful. Reinforcements to the old office building are also of vital importance since the new program brings with it new loading demands in the form of the exhibits, collections in storage, as well as visitors. None of the load bearing walls was touched and only the office partitions were removed to create the spacious new galleries.
New service annexes were created on the ground floor by extruding the base of the building outwards. While respecting the old edifice, this creates ample space in order for all mechanical and service essentials to be kept out of sight.
Despite the stylistic veneer of Antonio Toledo’s Neoclassical building, the architect and his team already had a sense of tall ceilings, generous windows, and the courtyard to make it work in a tropical setting. Some of the old partition walls featured large grill openings to facilitate cross ventilation. There is great comfort in the knowledge that the same sense of applicability germane to the original architecture continues as its metamorphosis steadily reaches fruition. Galicia reflects on reusing the old building: “There’s an energy embodied in the structure itself. In a sense we are really evolving the building. We’re learning from it. It gives us clues and tells us what to do.”
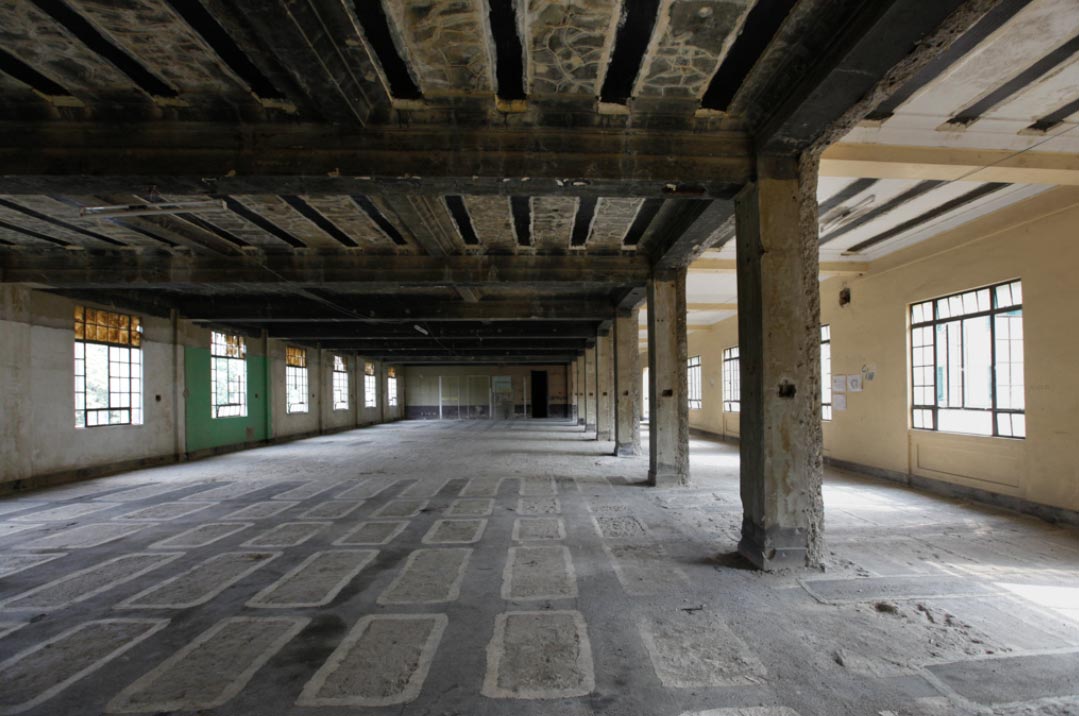
READ MORE: Makati’s newest memorial: The McMicking Memorial and Plaza, designed by Leandro V. Locsin Partners
The National Museum of Natural History will be a synthesis of traditional building and modern technology. It explores the relationship between old and new in terms of how a new life cycle for a historic edifice can be created not by imposing new dictates upon the old building, but by working with the ecology of the original in service of the new program. It will be born from a frame of mind that always seeks to be most resourceful and most sensitive to human comfort and the use of resources.
As I write this, I realize that the journey towards the realization of the project itself seems to trace the figure of a tree. There’s a central trunk to the narrative of this design evolution; branches and twigs each a possibility explored, pursued, developed and learned from. The manner in which everything goes back to the original concept is a testament to the appropriateness of the design—from oculus to trunk, to branches and everything. Every choice made in the creative process is organic and natural to the creature.
In evolutionary biology, natural selection remains the primary reason for successful adaptive evolution. In the case of The National Museum of Natural History, perhaps the same could be said about adaptive architecture as well.
This story first appeared in BluPrint Volume 2, 2015. Minor edits have been made for Bluprint online.
Images courtesy of Dominic Galicia Architects